APS系统软件对于生产制造型企业而言,可以很好的优化库存管理和提升生产交期时间,那么,APS系统软件是如何优化零部件库存管理的呢?下面,就跟着小编来了解一下吧。
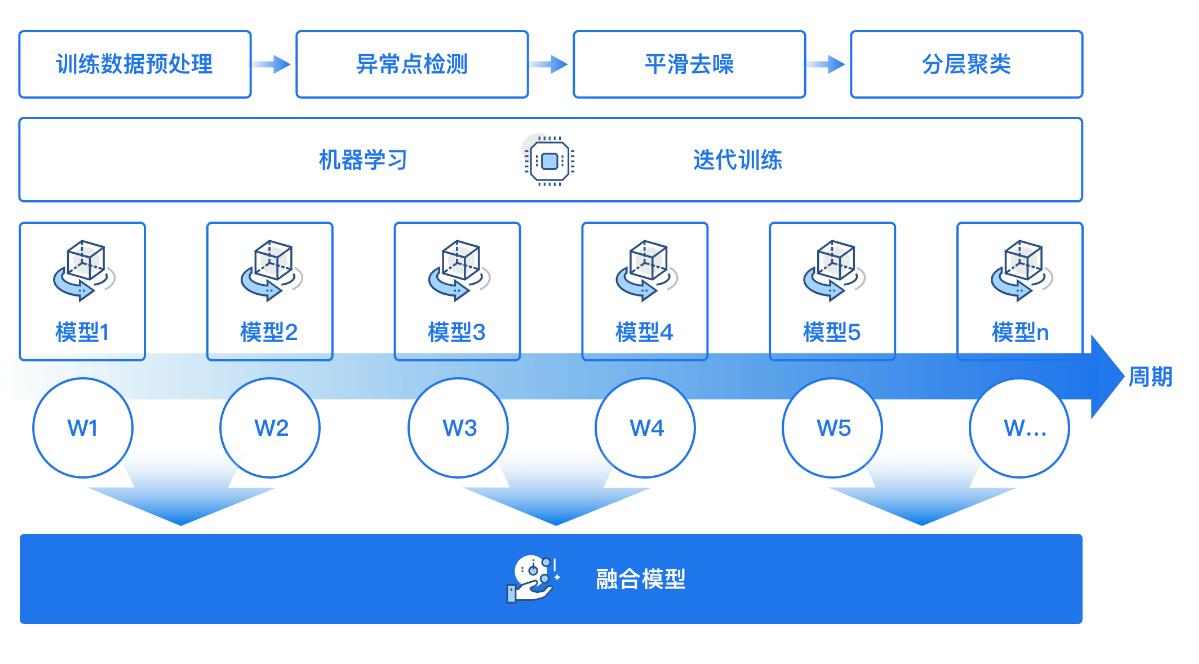
原则上,零部件的生产应该遵照成品组装计划安排。但是实际上,因为零部件的生产会提前于总装,经常有不能配套的情况发生。造成零部件库存过高或呆料的原因很多,主要包括几条:
总装因欠料发生计划变更。本来安排要装配的产品,因欠料临时延期,但是该订单的半品已经生产了。后面的工单被提前,但是半品的生产没有完成,又不能进行组装。多次修改计划,造成混乱。
APS系统软件中的按库存约束排程可以完全避免这种情况发生。组装工序的生产计划依据在库与在途库存约束制定,所有订单均排在齐料时间之后,因此不会发生因欠料临时延后的问题。半品的库存和未来几天的产出计划也作为总装排程中的约束条件,协同排程,避免了计划的频繁修改。
前后工序缓冲时间过长,工单整体生产周期太长,应对变化的能力变弱,零部件生产提前时间越长,组装段计划发生变化的可能越大;工序之间延迟时间与在制品数量是成正比的。半品大量堆积在车间内,易造成混乱也容易发生损坏
导入APS系统软件,首要的变化就是工序之间的缓冲时间大大缩短。在人工排程方式下,因为计划修改困难,计划员通过延长工序间缓冲时间的方式简化计算,一般都至少维持一个班次(12小时)的延迟。在导入APS系统软件后,工序之间的延迟时间缩短到2-4小时,生产周期整体缩短。使用APS排程后,半品生产一个工序完成后很快就转移到下一个工序,停留在车间产线边的数量和时间大大减少。同时,半品生产与成品组装之间的时间间隔也很短,成品订单变更的概率大大降低。